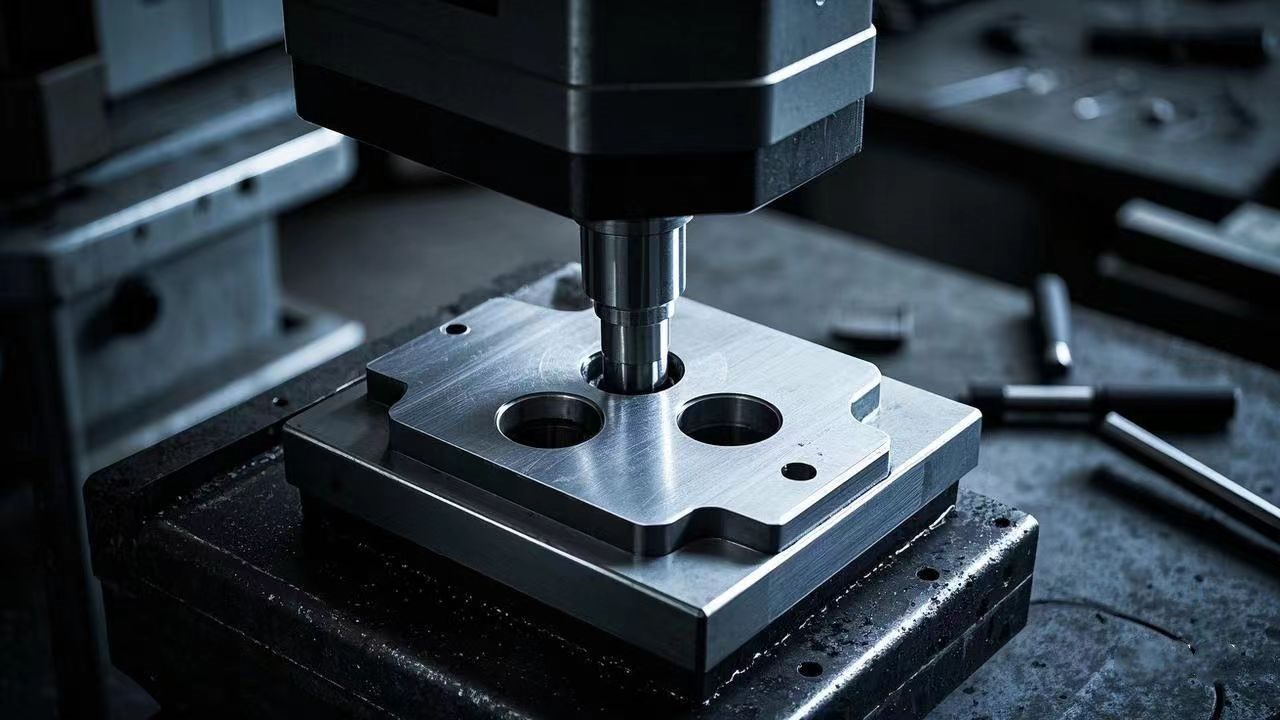
Cold Work Steel
Cold Work Tool Steel is primarily high carbon steels comprising comparatively low tungsten, chromium, manganese, and molybdenum additives to alloys. These improvements to alloy make it hardenable, making oil tempering with little deformity than with the W sequence. Such are comparatively affordable steels, and their high carbon composition provides sufficient strength to use for short-term implementations.Cold work tool steel basically is high carbon steel. The alloy contains tungsten, manganese, chromium, and molybdenum relatively low alloy steel. These alloys added to improve hardenability, allowing less distortion than the W series of quenching oil. These are relatively cheap steel, high carbon content they will produce sufficient wear resistance, used for short-term operations. It is used for all types of blanking and forming dies, gauges, fixtures, etc.
Cold work tool steel basically is high carbon steel. The alloy contains tungsten, manganese, chromium, and molybdenum relatively low alloy steel. These alloys added to improve hardenability, allowing less distortion than the W series of quenching oil. These are relatively cheap steel, high carbon content they will produce sufficient wear resistance, used for short-term operations. It is used for all types of blanking and forming dies, gauges, fixtures, etc.
In ASTM Steel standard Cold Work Tool Steel main include the “W” (Water Hardening), “O” (Oil Hardening), “A” (Medium Alloy Air Hardening), “D” (High Carbon, High Chromium) Tool Steel Series. Typical Steel Grade: W1, W2, W5 tool Steel; O-1, O-2, O6, O7 Oil Steel; A2, A4, A6, A7, A8, A9, A10, A11 Cold work Steel; D2, D3, D4, D5, D7 Steel; etc.
Equivalent grades:
STANDARD | INDIAN STD | CHINA | AUSTRIA | BRAZIL | SLOVANIA | SWEDEN | CHEZ | ITALY | JAPAN | S.KOREA | ||||||
---|---|---|---|---|---|---|---|---|---|---|---|---|---|---|---|---|
DIN | AISI | EST | BOHLER | VILLARES | RAVNE | ASSAB/UDDEHOLM | DEW | POLDI | LUCCHINI | VERONA | DAIDO | HITACHI | NIPPON | SANYO | DOOSAN | |
1.2379 | D-2 | SKD 11 | YTL122 | K110 | VD2 | OCR12VM | SVERKER21 | 1.2379 | 2002K | DUYOS2379 | 1.2379 | DC 11 | SLD | KD11V | QC11 | STD 11 |
Product Specification
MATERIAL | CHEMISTRY | Application | |||||||||||
AISI/ASTM | EN | DIN | JIS | C | S | P | SI | Mn | Cr | V | W | Mo | |
D2 | X155Cr Vmo V12.1 | 1.2379 | SKD11 | 1.45-1.60 | ≤0.03 | ≤0.03 | 0.10-0.60 | 0.20 - 0.60 | 11.00 - 13.00 | 0.70 - 1.00 | 0.90 | Shear blades, blanking punches, die chasers, rolls for cold mills treading rolls and chasers, molds for plastic materials. | |
D3 | X210Cr12 | 1.2080 | SKD1 | 1.90 - 2.20 | ≤0.02 | ≤0.03 | 0.10 - 0.40 | 0.15 - 0.45 | 11.00 - 12.00 | Rolls for cold strip mills and wire squeezer mills, dies for small metal parts, punching and drawing dies for sinterings. | |||
A2 | 100CrMoV5-1 | 1.2363 | SKD12 | 1.05 - 1.90 | ≤0.35 | ≤0.35 | 0.20 - 0.40 | 0.40 - 0.70 | 4.80 - 5.01 | 0.10 - 0.30 | 0.40 - 0.70 | Blanking dies, rolls, stamping dies etc. | |
O1 | 100MNCrW4 | 1.2510 | SKS3 | 0.90 - 1.05 | 1.00 - 1.20 | 0.5 - 0.79 | 0.5 - 0.70 | 0.40 - 0.60 | Dies, blanking punches, moulds for plastic materials. | ||||
DC-53 | 0.93 | ≤0.010 | ≤0.03 | 0.95 | 0.4 | 7.8 | 0.25 | 1.9 | threading rolls and dies, icy trimming, cutting, stamping tools, precision punching and cutting |
D2 (1.2379)
D2 is an air-hardening (cold work) Tool steel. high carbon, high chromium tool steel(HCHCr) with extremely high wear resisting properties. It is a very deep hardening steel and will be practically free from size change after proper treatment. The high percentage of chromium gives it mild corrosion-resisting properties in the hardened condition.
High-alloy steel for through-hardening with moderate machinability; extremely wear resistant and low warpage, good dimensional stability, toughness and through hardenability.
D2 ROUND BAR | D2 FLAT BAR | D2 SQUARE BAR | D2 PLATE |
D2 FORGED BARS | D2 ROLLED BARS | D2 PEELED or D2 BRIGHT |
Chemical composition:
CARBON C% | SILICON Si% | MANGANESE Mn% | CHROMIUM Cr% | MOLYBDENIUM Mo% | VANADIUM V% | PHOSPHORUS P% | SULPHUR S% | |
---|---|---|---|---|---|---|---|---|
AISI D2 | 1.4O-1.60 | 0.10-0.50 | 0.15-0.50 | 11.O-13.0 | 0.60-0.80 | 0.75-1.10 | ≤ 0.035% | ≤ 0.035% |
Application:
Blanking Dies, Forming Dies, Coining Dies, Slitting Cutters, Heading Tools, Long Punches, Forming Rolls, Edging Rolls, Master Tools, Beading Rolls, Intricate Punches,Extrusion Dies, Drawing Dies, Lamination Dies, Thread Rolling Dies, Shear Blades, Burnishing Tools, Gauges, Knurls, Wear Parts.
Physical Properties :
Density : at 20 °C 7,70 kg/dm3 Thermal expansion between : 20 °C and... °C, 10-6 m/(mK)
Thermal conductivity : | 100 °C | 200 °C | 300 °C | 400 °C | 500 °C |
20 °C 20,0 W/(m.K) | 10.5 | 11.0 | 11.0 | 11.5 | 12.0 |
Heat Treatment:
Annealing | 800 - 850 °C | ||||||||||||
Hardness after annealing | Max. 250 HB | ||||||||||||
Stress relieving | 650 - 700 °C | ||||||||||||
Hot forming | 1050 - 850 °C | ||||||||||||
Hardening | 1020 - 1080 °C | ||||||||||||
Quenching media | Oil, Salt bath ( 220 - 250 °C or 500 - 550 °C ) Air or compressed air | ||||||||||||
Hardness after quenching | 63 - 65 HRC | ||||||||||||
Hardness after tempering : |
|
The physical properties of D2 tool steels are outlined in the following table.
Coefficient of thermal expansionat °C | 2O-100 | 2O-200 | 2O-300 | 2O-400 |
---|---|---|---|---|
10-6 m/(m*K) | 10.6 | 11.5 | 11.8 | 12.3 |
Thermal Conductivity at °C | 20 | 350 | 700 | |
W/(m*K) | 16.7 | 20.5 | 24.2 |
D3 (1.2080)
Equivalent grades:
STANDARD | WELLKNOWN NAME | CHINA | AUSTRIA | SLOVANIA | SWEDEN | CHEZ | ITALY | ||
---|---|---|---|---|---|---|---|---|---|
DIN | AISI | EST | BOHLER | RAVNE | DEW | POLDI | VERONA | SANYO | |
1.2080 | D-3 | WPS | YTL120 | K100 | OCR12VM | 1.2080 | 2002 | 1.208 | QC1 |
Chemical composition:
ELEMENTS | CARBON C% | SILICON Si% | MANGANESE Mn% | CHROMIUM Cr% | PHOSPHORUS P% | SULPHUR S% |
---|---|---|---|---|---|---|
AISI D-3 | 1.9O-2.30 | 0.10-0.40 | 0.15-0.45 | 11.O-13.0 | ≤ 0.035% | ≤ 0.035% |
D3 ROUND BAR | D3 FLAT BAR | D3 SQUARE BAR | D3 PLATE / D3 SHEETS |
D3 FORGED BARS | D3 ROLLED BARS | D3 PEELED or D3 BRIGHT |
Physical Properties :
1.2080 Tool Steel Coefficient of Linear Thermal Expansion 10-6 OC-1
2O-100oC | 2O-200oC | 2O-300oC | 2O-400oC | 2O-500oC | 2O-600oC | 2O-700oC |
11.7 | 12.0 | 12.4 | 12.9 | 13.3 | 13.6 | 14.0 |
Heat Treatment:
Annealing | 800 - 850 °C | ||||||||||
Hardness after annealing | Max. 248 HB | ||||||||||
Stress relieving | Approx 650 °C | ||||||||||
Hot forming | 1050 - 850 °C | ||||||||||
Hardening | 940 - 970 °C | ||||||||||
Quenching media | Oil, Salt bath (500 - 550 °C ),Air or compressed air | ||||||||||
Hardness after quenching | 63 - 65 HRC | ||||||||||
Hardness after tempering : |
|
Application:
Forming rolls, drawing dies, forming, powder compaction tooling, and lamination dies.
Equivalent grades:
STANDARD | BRAZIL | AUSTRIA | SWEDEN | GERMANY | SLOVANIA | ITALY | JAPAN | S.KOREA | TAIWAN |
CHEZ. REP |
CHINA | AMERICAN | ||||||
MOULD STEEL |
VILLARES | BOHLER | AASAB | BUDERUS | DEW | GRODITZ | RAVNE | LUCCHINI | VARONA | DAIDO | HITACHI | NIPPON | SANYO | DOOSAN | GLORIA | POLDI | EST | AISI |
1.2510 | VND | K460 | - | - | 1.2510 | - | OW4 | - | - | GOA | SGT | KS3 | QKS3 | - | - | STABIL K | YTO-1 | O-1 |
Chemical composition:
CARBON C % | SILICON Si% | MANGANESE Mn% | CHROMIUM Cr% | TUNGSTEN W% | VANADIUM V% |
SULPHUR S% |
PHOSPHORUS P% | |
AISI O-1 | 0.85-0.95 | 0.20-0.40 | 1.0O-1.30 | 0.40-0.60 | 0.40-0.60 | 0.20-0.20 | ≤ 0.035% | ≤ 0.035% |
Application:
Blanking Dies, Bushings, Forming Dies, Master Tools, Forming Rolls, Gauges, Trim Dies.
Heat Treatment :
Annealing | 710 - 750 °C | ||||||||||
Hardness after annealing | Max. 220 HB | ||||||||||
Stress relieving | Approx 650 °C | ||||||||||
Hot forming | 1050 - 850 °C | ||||||||||
Hardening | 780 - 820 °C | ||||||||||
Quenching media | Oil, Salt bath (200 - 250 °C ) | ||||||||||
Hardness after quenching | 63 - 65 HRC | ||||||||||
Hardness after tempering : |
|
A-2:
Equivalent grades:
STANDARD | BRAZIL | AUSTRIA | SWEDEN | GERMANY | SLOVANIA | ITALY | JAPAN | S.KOREA | TAIWAN |
CHEZ. REP |
CHINA | AMERICAN | ||||||
MOULD STEEL |
VILLARES | BOHLER | AASAB | BUDERUS | DEW | GRODITZ | RAVNE | LUCCHINI | VARONA | DAIDO | HITACHI | NIPPON | SANYO | DOOSAN | GLORIA | POLDI | EST | AISI |
1.2363 | VA2 | - | - | - | 1.2363 | - | OA2 | - | - | - | - | KD12 | - | - | - | - | - | A-2 |
In cutting operations the toughness of AISI A2 steel gives excellent resistance to chipping of the cutting edge. In many cases, tools made of A2 steel have given better tooling economy than high-carbon, high-chromium steels of the D3/ W.-Nr. 2080 type. AISI steel A2 has much better machining and grinding properties.
A-2 is an air hardening (cold-work) tool steel with wear properties between O-1 oil hardening and O-2 air hardening.
This offers good toughness with medium wear resistance along with relatively easy machining. A-2 also has excellent non-deforming properties. These characteristics have made this steel a very popular and widely used material.
A-2 has a machinability rating of 65% of a 1% carbon tool steel and it is sold in the annealed condition. Typical annealed hardness is BHN 197/241 Rc 12/22.
With a maximum working hardness is BHN 698 Rc 62, A-2 is capable of meeting ASTM-A681.
Application:
Blanking dies, coining, cold forming, block and ring gauges, cold trimming and forming dies, cold shears, rolls, knurls and knurling tools, machine parts, mandrels, reamers, shear and slitter blades, punches and punch plates, stamping dies and threading tapes.
Chemical composition:
CARBON C % | SILICON Si% | MANGANESE Mn% | CHROMIUM Cr% | MOLYBDENUM Mo% | VANADIUM V% |
SULPHUR S% |
PHOSPHORUS P% | |
AISI A-2 | 0.95-1.05 | 0.10-0.5 | 0.3O-1.00 | 4.75-5.50 | 0.9-1.40 | 0.10-0.50 | ≤ 0.03% | ≤ 0.03% |
Heat Treatment:
Annealing | 800 - 850 °C | ||||||||||
Hardness after annealing | Max. 240 HB | ||||||||||
Stress relieving | Approx 650 °C | ||||||||||
Hot forming | 1050 - 850 °C | ||||||||||
Hardening | 950 - 980 °C | ||||||||||
Quenching media | Oil, Salt bath (500 - 550 °C ),Air or compressed air | ||||||||||
Hardness after quenching | 63 - 65 HRC | ||||||||||
Hardness after tempering : |
|
AISI S7
AISI S7 is a general purpose air-hardening tool steel with high shock and impact resistance. It has good resistance to softening at moderately high temperatures. This combination of properties makes it suitable for many hot work and cold work Application. Excellent combination of high strength and toughness. Useful in moderate hot work as well as cold work tooling. Added size stability when air hardened.
Application:
Bull Riveters, Concrete Breakers (Moll Points), Plastic Mold Dies, Cold Forming Dies, Riveting Dies, Powder Metal Dies, Notching Dies, Dowels, Drills, Drill Plates, Hubs, Blanking Dies, Bending Dies, and Master Hobs.
Chemical composition :
CARBON C % | SILICON Si% | MANGANESE Mn% | CHROMIUM Cr% | MOLYBDENUM Mo% | VANADIUM V% |
SULPHUR S% |
PHOSPHORUS P% | |
AISI S-7 | 0.45-0.55 | 0.2O-1.0 | 0.20-0.80 | 3.00-3.50 | 1.3O-1.80 | ≤ 0.30% | ≤ 0.03% | ≤ 0.03% |